As mini excavators get older the constant use means that regularly wearing parts such as the pins and bushings start to wear out. These are replaceable wearing parts and the following article gives some tips and tricks around some of the challenges around replacing them.
If you are just looking to purchase digger bucket pins Click Here
How to replace digger link pins / boom pins / ram pins
As a start all pins will be secured into their position but the way this is done varies from machine to machine. Takeuchi diggers tend to have a large nut and washer on the end of the pin, Kubota and JCB Diggers often have a hole drilled in the end of the pin and a bolt is secured down through it. Other machines have a thread in the end of the pin which a bolt is screwed into. Whatever the type on your excavator this needs to be removed, and then the pin should be able to be removed.
With the pins at the dipper end of the machine, removing them is normally fairly easy but as you get further up the dipper arm and through the boom to the kingpost you need to start to ensure that the arm is well supported before you start to remove the pins.
Often if you are removing the boom to replace the kingpost bushes you will need an overhead crane or a sling on a forklift to assist with removing it and getting it back into position again.
Once the pins are removed it is time to work on the bushes. We always recommend replacing both the pins and the bushes together as both will wear together over time so only replacing one part can often lead to bigger problems.
How to remove digger bushes
The first challenge when replacing the bushes in the arm of your excavator is to remove the old bushes.
Typically if you are at the point of removing them, then they are worn out so it doesn't matter what damage you do to the old bushes but you really want to preserve the integrity of the digger arm at all costs.
We have pulled together a few tips and tricks from plant fitters to help you out!
1) Brute Force! A good old hammer and bar is often enough on smaller excavators especially if the bushes are quite worn out. Be sure to use a bar that is larger than the internal diameter of the bush but smaller than the outside diameter. If you are doing it regularly some engineers find it handy to create a stepped tool for the various sizes of bush.
2) Weld a stub into the bush (even a large blob of weld can work), and this allows you to put a bar through the bush and knock it out
3) Weld around the radius of the bush - this really applies to larger bushes and the idea is that as the weld cools it shrinks the bush enough to allow it to be removed easily
4) Cut the bush out - using an oxy-acetylene torch or similar it is possible to cut a slot into the wall of the bush which then allows the bush to shrink and be easily removed. A word of caution on this - it is very easy to go too far and cut into the arm of the digger and cause expensive damage!
5) Hydraulic Press - probably the safest option but we have put it last in the list, as not everyone has access to the equipment necessary for this.
How to replace digger bushes
Having removed the old bushes from the arm of your digger, then next step is to fit replacement bushes.
Again there are various ways of doing this with varying levels of equipment required depending on what equipment you have on hand.
1) Hammer them in! It works...sometimes. But be very careful - excavator bushes are normally manufactured from Induction Hardened Steel which although very hard and wear resistant is susceptible to splitting off when you are hammering them.
2) Apply Heat - this works quite effectively if you can get the heat source close enough to where you are replacing the bush. Essentially you need to heat the bush housing as hot as you can which expands it and allows you to push the bush in by hand and let it cool again until it is tight. Just watch the paintwork on the arm of the digger as the heat can do considerable damage to this.
3) Cool the Bush - effectively this works in the reverse of the above method but rather than heat the housing (which expands it) you cool the bush which contracts it. Typically, trained engineers do this with Liquid Nitrogen which is -195 °C and this requires very specialist equipment and training to use. If it is a small excavator, it is worth putting the bushes into a freezer 24 hours before you try and fit them as often this will cool them enough to make the job a lot easier.
4) Hydraulic Press - again this also requires specialist equipment to do but is a safe and effective way of fitting bushes. It is sometimes used in conjunction with method 2 or 3, especially on larger excavators.
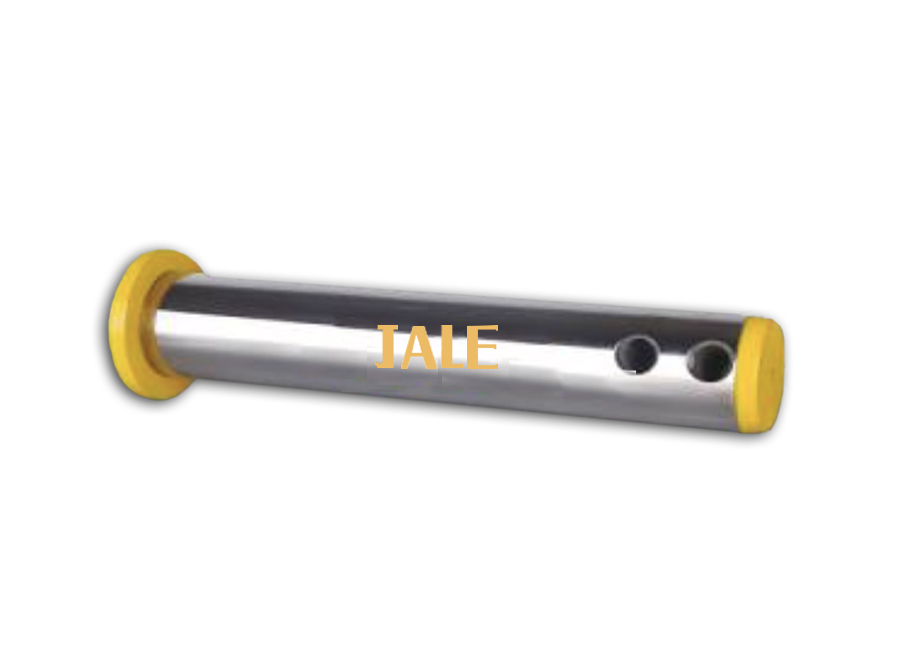
Post time: Jul-19-2022